Energy Management
Implemented Digital ISO 50001 Intelligent Management to Enhance Green Energy Efficiency
Upholding the energy policy: smart carbon-reduction, resource circulation, and environment conservation, by implementing the ISO 50001 energy management system, we achieve energy management and verify energy efficiency and the achievement of energy conservation targets of all sites. To achieve the 1% annual energy conservation target, we propose energy conservation programs every year, use high-performance cogeneration, build renewal energy equipment, optimize existing equipment, and combine smart systems to make constant innovation to optimize the performance in energy conservation and carbon reduction. We also set emerging environmental protection benchmarks to actively transform into a "new low-carbon & green energy paper company".
We applied the ISO 50001 energy management system to the Paper Division in 2013 and then introduce it to all the Operational Sites in Taiwan in 2015. The headquarters established a cross-department Energy Management Committee to ensure energy management to be developed towards the goals of continual improvement. We awarded in public and got the related awards from the government to encourage the employees to figure out the opportunities to energy-saving improvements and increase the benefits of the energy. To systematically manage energy performance, we initiated the ISO 50001 energy management system in our overseas companies in 2022. After the Binh Duong paper mill in Vietnam received certification in 2022, 8 paper container plants, including Zhonghao Plant in Shanghai, China, obtained certification in 2023. We will continue expanding this system to our overseas operations and conduct regular annual verifications to ensure effective smart energy management.
The electricity and steam at CLC are primarily used for production equipment and utility systems. Utilizing ISO 50001 management tools, intelligent management, and cross-plant energy efficiency benchmarking, the company strives to optimize the operational efficiency of each paper machine. In 2023, the energy emission intensity of the parent company's paper container division remained steady at 0.61 (GJ/1,000 sqm) compared to the previous year. However, due to overall market downturns and the optimization of the new biomass boiler at the Chupei Mill, the energy emission intensity for the industrial paper, household products, and paperboard divisions slightly increased to 8.86 (GJ/MT paper) and 16.59 (GJ/MT paper), respectively. The cumulative energy consumption per unit product increased by 3.93%* compared to the base year of 2019. Despite this, the company continued to invest NT$91.43 million in 44 energy-saving projects across 3 categories: process improvement, equipment improvement, and energy management. These efforts resulted in an annual electricity saving of 13,889,310 kWh, a reduction of 8,343 tCO2e emissions, and approximately NT$72.04 million in energy cost savings.
* After calculating the energy improvement rate of each mill/plant (= annual reduction rate), we convert it into the proportion of each mill/plant according to the calorific value of the energy used by each mill/plant, then add up the improvement rate of each mill/plant* the proportion of each mill/plant = the improvement rate of the whole company (The value is also the unit product energy consumption of whole company).
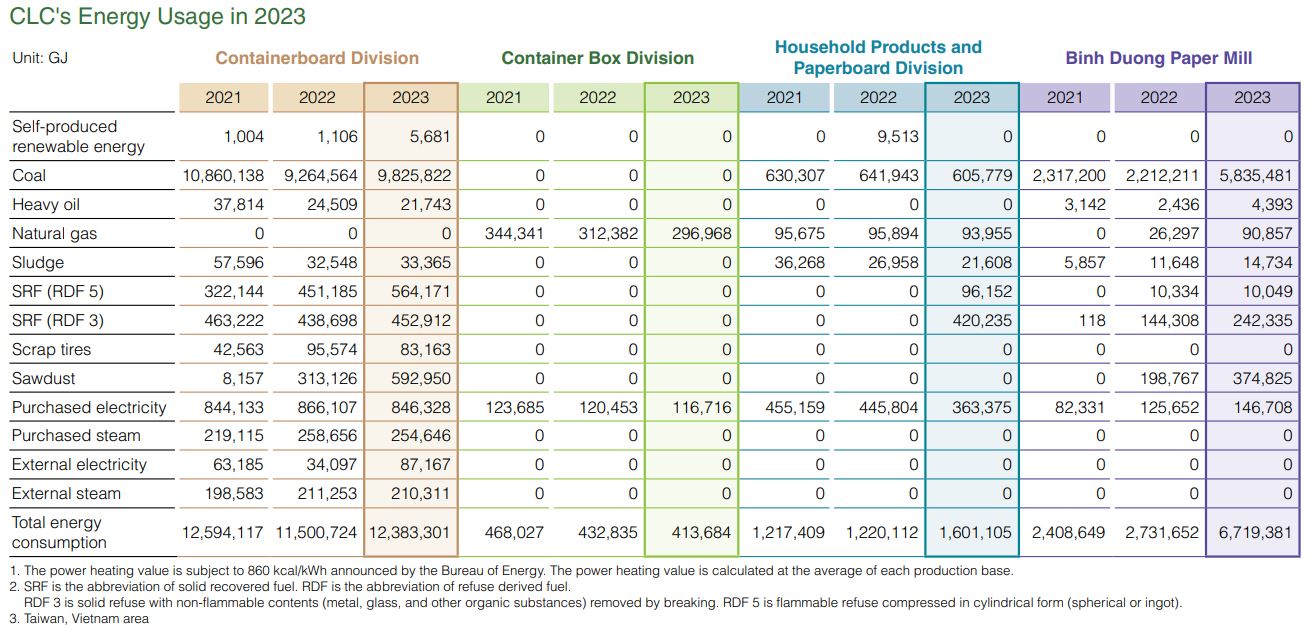
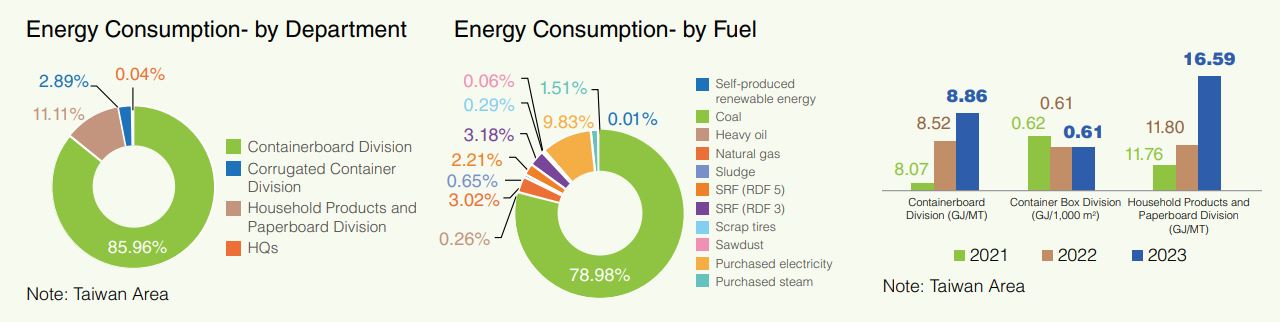
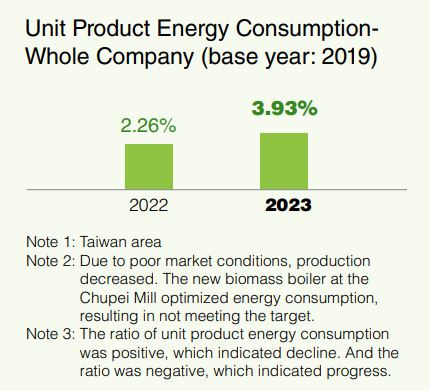
Actively Developing Renewable Energy to Seize Green Energy Opportunities
Increasing Renewable Energy Capacity: Surpassing Major Electricity User Regulations, the Only Industry Player to Obtain Wind and Solar Renewable Energy Certificates
CLC has utilized the geographical and production line characteristics of its various mill/plant locations to establish wind, solar, and biogas renewable energy sources. In 2022, the total installed capacity of renewable energy across Taiwan nearly doubled compared to 2020, reaching an overall renewable energy generation capacity of 12,056 kW. In 2023, the Houli Mill added solar photovoltaic and biogas green electricity installations, further increasing capacity by 2,000 kW. Currently, the renewable energy installed capacities at the Chupei and Houli Mills have both met the 2025 goal of 10% renewable energy capacity for major electricity users ahead of schedule.
1st Paper Company to Invest in Wind Energy and Obtain Renewable Energy Certificates
(Accumulated 12,575 Certificates)
Since introducing Taiwan's 1st and then-largest wind turbine in Asia in 2003, CLC became the 1st and only paper company in the country to obtain wind renewable energy certificates in 2017. CLC continues to install solar and wind renewable energy systems based on the geographical characteristics of its mill/plant locations. In 2023, it became the only paper company to simultaneously obtain wind and solar renewable energy certificates, with a cumulative total of 12,575 certificates, equivalent to the annual electricity consumption of 3,493 households (based on Taiwan Power Company's published average monthly household electricity usage of 300 kWh over the past 10 years).
Waste-to-Energy: Biogas Power Generation at Tayuan and Houli Mills
In 2022, CLC's Tayuan paper mill officially began commercial operation of two 1,200 kW gas-fired engine generators, with an annual electricity output of 13 million kWh. The mill also installed waste heat recovery boilers to convert the waste heat from the generator exhaust into steam for use in the paper-making process within the mill. By utilizing biogas for power generation and steam production, the mill reduces greenhouse gas emissions by up to 14,000 tCO2 equivalent annually. To further enhance green energy and achieve net-zero emissions, the flagship Houli Mill in Taiwan is currently constructing a biogas green electricity system (2,000 kW, estimated annual electricity output of 10.56 million kWh, reducing carbon emissions by 7,660 t).
Leading the Industry in Cogeneration Applications and Management, Establishing an Intelligent Energy-Saving Demonstration
Since introducing the 1st large-scale cogeneration equipment in the paper industry in 1984, CLC has once again led the industry by implementing intelligent management for the G3 cogeneration boiler at the Houli Mill in 2019. This technology has been progressively deployed across the company, including 4 high-efficiency cogeneration systems at the Houli and Tayuan paper mills. By optimizing boiler monitoring, extending maintenance intervals, eliminating temporary failures, and improving both cogeneration and power generation efficiency, CLC has set a benchmark in intelligent energy-saving practices, earning widespread recognition.
Houli Mill Awarded Taichung City's Environmental Protection Bureau's "Air Pollutant Reduction Incentive Program"
In 2023, the Houli Mill's cogeneration boiler (130 MT/h) actively replaced coal with low-pollution wood pellet fuel, reducing coal usage by a total of 14,259 MT and cutting carbon emissions by approximately 32,795 tCO2e per year. The mill received recognition in the 112th Taichung City Air Pollutant Reduction Incentive Program and was awarded NT$700,000.
Deepening the Application of Low-Carbon Circular Alternative Fuels to Accelerate the Transition to Net Zero
In Taiwan, 98% of energy relies on import. To enhance energy efficiency and reduce the dependency on fossil fuel, we actively develop various types of alternative fuels, such as using process residual materials to increase the quantity and improve the quality of alternative fuels with technology, in order to enhance the utilization rate of alternative fuels.