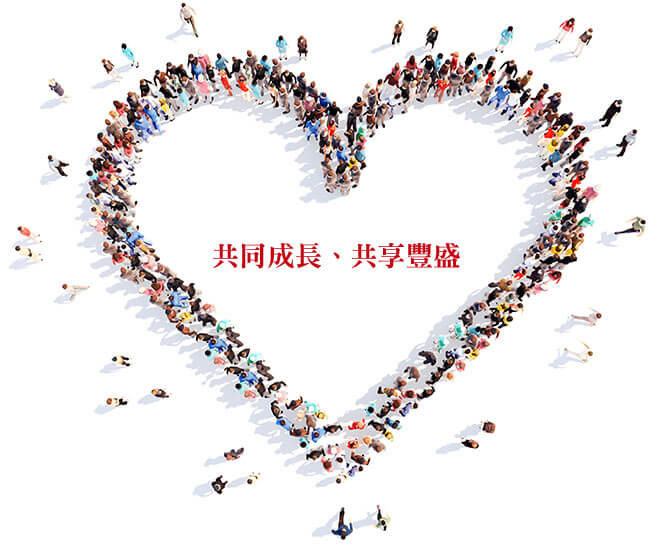
Friendly Workplace
We value our commitment to employees,
by building a happy and healthy workplace, and creating a challenging work environment
suitable for sustainable learning, to grow together with our people.
Diversity and Equal Opportunity
● Strategy: Provide competitive salaries and sound benefits to attract outstanding and diversified talents, and realize workplace equality.
Goals of 2030:
● Raise the average employee salary by 10% vs 2020.
● Diversify employee benefits
● Cultivate young management
Human Resources Strategy: Realizing Global Localization of Key Talent
CLC continually attracts outstanding individuals to join its team through a competitive compensation system and comprehensive training programs. Guided by the principle of "loyalty and integrity," the company aims to cultivate partners who identify with its corporate culture, vision, and core values.
Employees are key to sustainable operations. Focusing on long-term talent development, we keep abreast of salary and labor market trends, comprehensively considering its medium- and long-term development strategies and annual business performance. Employee compensation and benefits are adjusted on a rolling basis. By attentively listening to employees' needs, CLC continuously optimizes its compensation-related systems, hoping that through shared happiness, it can promote sustainable prosperity for both its talent and the company.
Enhance female power, the proportion of female employees increased to 13% in Taiwan and 22.3% for Whole group
By the end of 2023, the number of employees across major operation base (Taiwan, China and Vietnam) were 6,751 persons, increasing 36 persons. For Taiwan district, there are 3,680 employees, including 2,859 labor staff, 688 management staff, and 153 senior officers* hired 100% from Taiwan. The overall number of employees decreased 49 persons. Due to the characteristics of the paper industry, male employees are traditionally higher than female employees, however, more female staff are hired in the production, technology, R&D, and marketing departments in recent years. In 2023, the proportion of female employees increased by 0.3% to 13.3% in Taiwan, and 22.4% for Whole group. Despite the significant gap between male and female employees, we always put competence first in talent recruitment, employment, and development and maintain equality and fair treatment of employees regardless of nationality, gender, race, religion, color, age, sexual orientation, marriage, and political affiliation. Therefore, no discrimination was reported in 2023.
*Senior officers are "first-level of supervisor"
Value Human Rights and Development Diversity
“Through fair and open recruitment channels, all employees are entitled to equal
rights and benefits regardless of gender, race, and nationality, in order to protect basic human rights.”
Human Rights
The Company's business bases in various places strictly abide by local labor regulations, are committed to protecting the basic human rights of all employees, and support and declare to the basic spirit of international conventions while formulating CLC's human rights policy in accordance with their guiding principles, so that all relevant people can be treated fairly and with dignity, including "tolerance of diversity and anti-discrimination, ban on child labor and prohibition of forced labor etc."
To ensure employees have a comprehensive understanding of human rights, CLC promotes relevant information through the EIP internal website, internal publications, and the E-Learning online learning system. Emphasizing workplace equality and communication, we continuously organize related seminars and promotes friendly workplace projects, including revising the "Sexual Harassment Prevention Act." From 2021 to 2023, 4 courses (13 sessions) were conducted, with a total of 636 participants, continuously enhancing communication and management skills. CLC also established mechanisms for preventing workplace sexual harassment and corruption. The internal website features an employee opinion mailbox and complaint channels, providing avenues for reporting unethical behavior and corruption.
Equal Employment
We followed the "People with Disabilities Rights Protection Act" and "Indigenous Peoples Employment Rights Protection Act" and hired 40 persons with disabilities and 27 indigenous people. In order to promote multiple employment, we have set up the "Bonus for Indigenous Long-term Employment". In 2023, a total of 24 eligible colleagues have applied. Not only do we encourage the indigenous peoples to work in CLC, but also hope that employees can serve for a long time. In terms of workforce composition, most CLC employees are Taiwanese, and we prioritize employment for local residents at individual production bases. Besides creating local job opportunities and stimulating domestic economic development, this policy also helps stabilize workforce. To ensure the well function of production line, we only hire a small number of foreign workers for the vacancies that cannot be filled by local citizens.
A Younger Workplace, 12 % of Female Employees with Seniority below 5 Years Have Been Promoted
As the paper industry is one of the traditional manufacturing industries dominating by male employees in the past, most members of the junior management are male, resulting in a ratio of about 10.9:1 in terms of male and female. There are 404 team or group leaders in Taiwan in 2023. For employees with seniority below 15 years, it takes about 7 years to become a team or group leader. Due to the transformation into a service industry and valuing innovation, younger people have been promoted to the junior management in recent years. We also actively promote the training plan, and optimize the management organization. Following the rise of equal opportunity in employment, since 2018, 46 employees with less than 5 years of seniority have been promoted to junior management positions, with 13% of them being female. This represents a significant change from the period of 2014 to 2017.
Implement Cultivation Programs for a Younger Management to Optimize the Management Organization
● Elite Staff Job Rotation and Training Plan
Every year, CLC selects elite talents based on employees' job performance to undergo rotations and other planning to cultivate diverse skills. Depending on their performance, they may be promoted to managerial positions for further development of their management capabilities.
● Talents Recommendation and Training Planning System
We are committed to building a well-established talents cultivation system and planning learning and development courses and training plans by level based on the organizational development and competency diversity. In recent years, we have been implementing key talents training programs. In 2023, we establish the Elite Recommendation and Development System for supervisors to develop potential talents.
● Paper Product Overseas Staff OTJ Courses
Trainees are selected through self-nomination and recommendations from unit supervisors, focusing primarily on practical on-the-job learning, supplemented by classroom courses. We have completed the planning of 18 courses (30 sessions) for managerial-level classroom training. The courses are tailored to the educational and experiential backgrounds of the trainees, with training durations ranging from 6 months to 2 years.
Suitability and Retention
We respect personal traits and expertise in employment and salary is according to their academic attainment, past experience, professional knowledge and skills, and professional seniority and experience. To retain excellent talents, through transparent policies including promotion, transfer, external training courses and resources, and the excellent talent pool, we encourage employees to take challenges and training to become management assistants. Medium- and higher-level supervisors at different management levels can also enjoy additional benefits including supervisor health checkup allowance and vehicle purchase allowance, and so on. In 2023, there were 348 new employees, with an employment rate of 9.4%. The male-to-female ratio of new employees in all employees was 9.2%: 10.8%.
*Note: For more information about the age distribution and regional breakdown of new employees at CLC, please refer to the appendix - Employee Information List.
People Oriented, Right People in the Right Place
Maintaining a Reasonable Turnover Rate
Suitable personnel turnover is necessary for enterprises to pursue sustainable development. In recent years, apart from maintaining a 10% reasonable turnover rate, we constantly recruit new employees to bring in vitality and diversify. In 2023, a total of 406 employees or 11% resigned, in terms of gender among all employees, 11% were male and 10.6% were female. In view of the increasing trend of aging retirees in recent years and the overall labor shortage in the market, our company will continue to participate in employment fairs across various regions, deepen industry-academia cooperation, and recruit new employees.
To effectively retain employees, we actively interview those filing their resignation and provide them with information about the internal job openings to facilitate the adaptive development of employees, reduce the impact of adaptation to job transfer, and to lower the overall turnover rate.
Online Anonymous Survey
In 2019, we began to conduct the online anonymous survey of the resignation procedure to discover, and review related problems and propose countermeasures, in order to provide a reference for the future amendment and adjustment of related management regulations or the welfare system. We received 223 responses till now.
Re-employment of Senior Employees
In response to macro-environmental changes, such as population aging and talents discontinuation, we are committed to building a workplace culture allowing the accumulation of professional knowledge and experience and respect for excellent employees to continue their contribution after the retirement age. In 2023, a total of 21 employees reached the retirement age. During 2018~2023, we hired 7 retirees as short-term consultants.
Well-Developed Retirement System
To ensure a secure retirement for our employees, CLC follows the Labor Standards Act and the Labor Pension Act, allocating retirement funds to both a specialized trust account with the Bank of Taiwan and individual employee accounts. Additionally, we have established the "Employee Retirement Implementation Plan." Each year, we proactively hire an actuarial firm to assess whether the balance in the annual retirement reserve accounts is sufficient, ensuring the protection of our employees' rights. In gratitude for their long-term dedication and contributions to the company, the supervisors of the respective units personally present a "Merits for CLC" retirement medal to each retiring employee.
Leading the Industry, Employee Profit Sharing and Encouragement for Investment with Participate Rate > 50%
To share our business performance results and encourage employees to develop saving habits, CLC has been a pioneer in the industry by promoting the "Employee Stock Ownership Trust (ESOT)" since 1998. Employees are encouraged to voluntarily allocate a certain amount to a trust account each month, with we contributing an additional 40% of the employees' contributions to the account for the purchase of CLC stock. Over the years, the participation rate in the ESOT has exceeded 40%. In 2023, the voluntary participation rate reached 50%, an increase of 2.1% from the previous year, with the subsidy amount reaching NT$40.52 M. Over the past 3 years, the total subsidy amount has reached NT$114.83 M.
Labor-Management Meeting and Labor Union
We hold the quarterly labor-management coordination meeting at each mill/plant to promote labor-management communication and strengthen a reciprocal relationship. We also have 2 internal labor unions (Chupei Mill and Hsinchu Mill). Besides the annual member meeting, the labor unions also hold the quarterly director and supervisor meeting to properly handle and follow up all suggestions made by the labor representatives at the meeting to respect and properly deal with the challenges and difficulties that employees face at work. All mills/ plants held Labor-Management 44 Meetings in 2023.
Listening to Employee Opinions
We value the opinions of employees and provide various channels for employees to express their claims, including the quarterly labor-management meeting, annual employee opinion survey, new and resigned employees’ opinion collection, labor union, and the anonymous communication channels on EIP internal website.
Employee Opinion Survey
● Collaboration with 104 Job Bank for Employee Sentiment Survey (Leading the Industry)
To enhance employees' sense of belonging and commitment to the organization, we value employees' feedback and collaborates with 104 Job Bank to conduct employee sentiment surveys. These surveys comprehensively collect employees' opinions and assess the appropriateness of strategic regulations. Based on the survey results, we take improvement measures and will continue to conduct surveys periodically to keep listening to employees' voices.
✓2019: 1st employee sentiment survey, systematically collecting employee opinions as a reference for decision-making.
✓2020: Expanded collection to include feedback on "workplace environment," "career development," and "supervisor encouragement."
✓2021: Added feedback areas such as "colleagues" and "corporate culture"; introduced incentive mechanisms to increase response rates.
✓2022: Continued to improve "workplace environment," "career development," and "supervisor encouragement" based on the 2021 survey results.
✓2023: Included "sustainable development" as a new evaluation area.
● Employee Sentiment Survey: Maintaining High Satisfaction with an Effective Response Rate over 45%
The headquarters' management office has initiated cross-functional teams to respond to the survey results, address employees' expectations, and set optimization goals and action plans. These efforts are integrated into HR strategies and planning, with the following concrete outcomes:
.jpg)
.jpg)
Salary and Treatment
Besides employee salaries are higher than the local minimum wage by 27% for bachelor’s degree and 39% for master's degree, we promote gender equality and equal pay for equal work. As male employees are generally more senior than female employees in some grades and have longer overtime work, the pay is different between male and female employees. Every year we review company’s business performance and make the salary adjustment based on the commodity price, resulting in the raise of the employee’s salary for 17 years at 1~3% each year, and up to 1% in 2022. In addition, wage of the non-management full-time employees is around NT$844 thousand, and the mean wage of full-time is around NT$786 thousand.
Employee Benefits
Better than the regulations: Expenses on employee benefits up to NT$44,000
We are committed to establishing employee policies in conformity with the related laws and regulations and welfare better than the regulations including health examination and various leaves for each CLC employee to receive full and proper care and concern. We also take care of the life of employees with various benefits. The employee welfare committee hold committee meetings and review the welfare system regularly ,and constantly develop comprehensive and complete employee care solutions. In 2023, we spent about NT$44,000 on the benefits of each employee. In addition, we awarded 《Happy Enterprise Award》- Gold for the 4th time which held by 1111 Job Bank.