Action for Climate Change
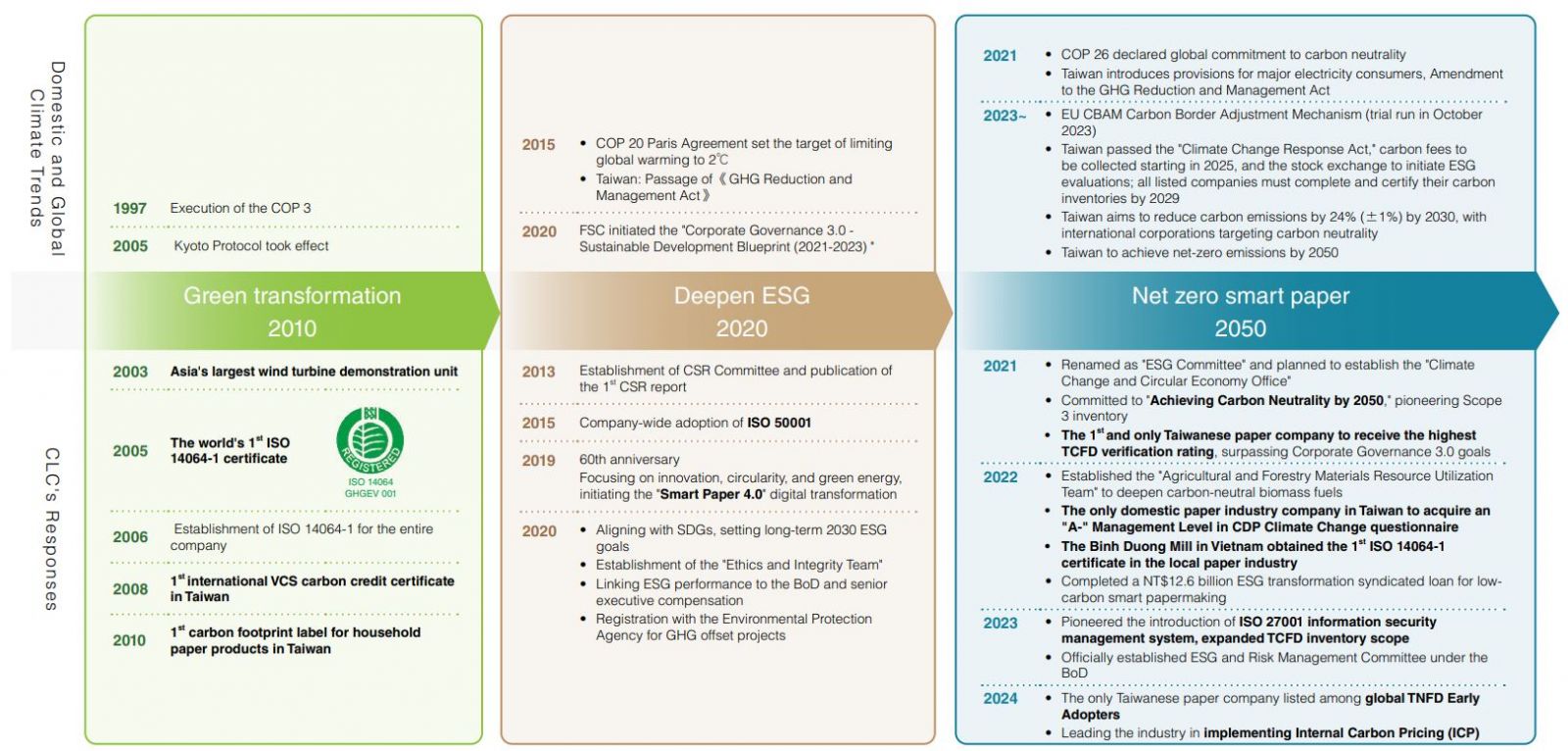
Expanding TCFD Scope, Implementing Internal Carbon Pricing (ICP), and Enhancing Climate Resilience
Circular economy practices are pragmatic steps towards global low-carbon and net-zero goals. Our company views climate change risks as opportunities and focuses on the core concept of "S.M.A.R.T. Low-Carbon Intelligent Paper," actively establishing circular economy bases domestically and internationally. We are committed to recycling paper for regeneration, focusing on "paper" as a natural-based solution, and leading the industry in emphasizing sustainable climate governance to enhance operational resilience to climate change. Since obtaining the world’s 1st ISO 14064-1 greenhouse gas inventory certificate in 2005, CLC has initiated emission reduction management on production lines, spearheading the promotion of low-carbon transformation. In 2008, we obtained Taiwan's 1st carbon credit trading certificate, in 2010, the 1st carbon footprint label for household paper products, and in 2023, we formed a national decarbonization team with the industrial chain, achieving the 1st industrial paper product carbon footprint inventory in Taiwan to accelerate grasping zero-carbon transformation business opportunities.
Exceeding the Financial Supervisory Commission's Corporate Governance 3.0 goals, CLC became the 1st Taiwanese paper company to pass TCFD verification and receive the highest certification rating in 2021. In 2022, we initiated greenhouse gas inventories for our domestic and international subsidiaries, with our Vietnam Binh Duong paper mill achieving the local industry's 1st ISO 14064-1 greenhouse gas inventory certificate. Enhancing our group's carbon management, by 2023, in addition to the Vietnam Binh Duong paper Mill, the Vietnam Vina Tawana Plant, China Shanghai Chung Hao Plant, and 7 other plants, as well as Gemtech Optoeletronics Corp. , have completed greenhouse gas inventories, with 80% completion for consolidated subsidiaries. We aim to achieve 95% completion by 2024. Committed to enhancing climate sustainability resilience, since 2022, we have been completing the CDP Climate Change Questionnaire, receiving a management-level rating in 2023. We will continue to strengthen carbon management to accelerate low-carbon development and climate adaptation strategies. Emphasizing natural growth, in 2024, our company will also respond to the "Taskforce on Nature-related Financial Disclosures (TNFD)," becoming the 1st Taiwanese paper company invited as a TNFD Early Adopter.
CLC Listed for 2 Consecutive Years in CommonWealth's "Corporate Carbon Reduction Thermometer," Meeting the Paris Agreement's 1.5˚C Temperature Control Goal
CommonWealth Magazine established the "Corporate Carbon Reduction Thermometer Platform" in 2022, aiming to inventory Taiwanese companies' carbon reduction commitments using international standards (meeting the Paris Agreement's goal of limiting global temperature rise to within 1.5˚C by the end of this century). In 2023, data from 725 companies were collected, and through model verification, including CLC, only 92 companies (12.6%) met the Paris Agreement's 1.5˚C temperature control goal. According to the latest report in June 2024, CLC's temperature rating was 1.485˚C, 0.003˚C lower than 1.488˚C in 2023, indicating our company's continuous progress towards the Paris Agreement's 1.5˚C goal.
In response to global carbon tariff trends (EU CBAM implementation, U.S. Clean Competition Act 2nd reading, etc.) and Taiwan's Climate Change Response Act incorporating the net-zero target into law with carbon fees to be imposed from 2025, CLC initiated TCFD reevaluation in 2023, expanding the inventory scope to include all operating sites in Taiwan, identifying 6 transition risks, 2 physical risks, and 4 climate-related opportunities, and taking corresponding measures to mitigate operational impacts. We will regularly monitor significant changes in international climate and carbon-related policies and continuously update TCFD evaluations. In 2024 Q1, we will formally launch the ICP internal carbon pricing introduction plan to accelerate our response to international decarbonization trends.
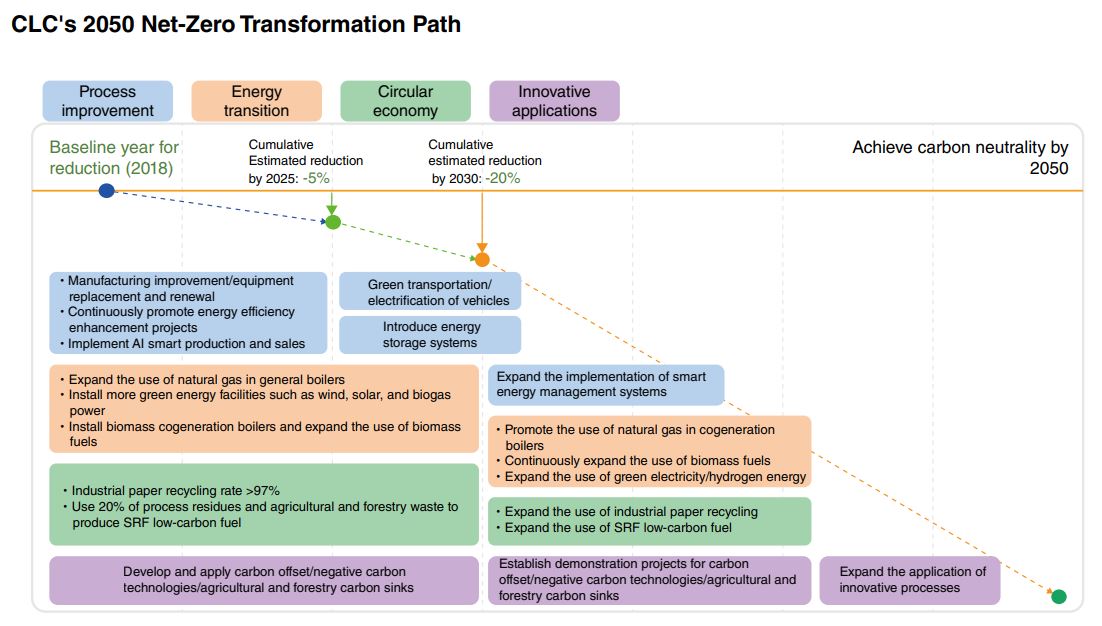
CLC Important milestones on climate governance
Long-term focus on climate change adaptation and mitigation strategies, ahead of the Financial Supervisory Commission's corporate governance blueprint, in 2021, CLC became the only company in Taiwan's paper industry to receive the highest TCFD third-party verification rating. In 2023, in response to significant domestic and international climate policy trends, CLC conducted a TCFD reevaluation and expanded the scope to include all operational sites in Taiwan. At the same time, the original Sustainability committee was elevated to the board of directors' oversight level to deepen the group's ESG management.
Emphasizing Nature Positive growth, in 2024, CLC responded to the "Taskforce on Nature-related Financial Disclosures (TNFD)," becoming a global TNFD early adopter, continuously expanding its focus on natural ecological issues. Additionally, CLC pioneered the introduction of Internal Carbon Pricing (ICP) within the company, steadily progressing towards the vision of achieving carbon neutrality by 2050.
I. Climate change management
Based on the core elements of TCFDs, CLC introduces the management framework and review the orientation and progress to climate change quarterly.
II. Climate change strategy
Engaging in green production over time, CLC annually reviews the overall effectiveness of our carbon reduction efforts through the third-party verification of our greenhouse gas (GHG) inventory results, with the goal of becoming a new low-carbon and green-energy paper company. We continuously align with international initiatives to mitigate and adapt to climate change.
Given that our major sources of GHG emissions are from Scope 1 (direct emissions from production processes) and Scope 2 (indirect emissions from electricity use), CLC focuses on energy management, aiming to enhance energy conservation and carbon reduction in our processes. From 2013 to 2023, we executed 480 energy conservation projects with an investment of nearly NT$700 million, achieving a substantial carbon reduction of 77,337 tCO2e. We are the only company in the industry to have obtained renewable energy certificates for both wind and solar power. Leading the industry, we have also introduced AI smart management, integrating offline digital inspection systems to expand the scale and efficiency of green production and sales through digitization, making us the 1st paper company in Taiwan to implement intelligent production and sales.
To accelerate the group's net-zero transformation, CLC has established 4 major scientific pathways for carbon reduction: improving energy efficiency, developing renewable energy, deepening the use of circular low-carbon fuels, and innovating the application of carbon-negative technologies. We have collaborated with National Chung Hsing University to establish Asia's 1st "Circular Economy Research Institute," actively investing in the recycling and reuse of agricultural and forestry residual materials. This initiative has pioneered the 3R PLUS Total Resource Circulation carbon reduction manufacturing chain, laying out a circular low-carbon biomass material ecosystem. In 2023 Q1, we also partnered with National Central University to promote the potential assessment and future business model research of the Tayuan Carbon Sequestration Demonstration Site, establishing the nation’s 1st Carbon Capture, Utilization, and Storage (CCUS) model, steadily progressing towards the 2050 carbon neutrality goal.
Core Element | Management Strategies and Actions |
---|---|
Governance | • The BoD has established the "Sustainability Committee," which integrates climate action resources and progress across departments. Under this committee, the "Climate Change and Circular Economy Office" has been established, with the General Manager serving as the convener. This office actively manages climate change issues and takes action, reporting to the Board of Directors quarterly. |
• The BoD and the management team are responsible for approving climate-related strategies, goals and specific actions. | |
Strategy | • Continue to implement climate change mitigation and adaptation projects. |
• Promote smart production and sales and a green energy circulation, and transform the company into a low-carbon and green energy paper company. | |
Risk Management | • The BoD has established the "Risk Management Committee," which collaborates across departments to identify climate-related risks and opportunities. |
• Quantify financial impacts, devise countermeasures. | |
• Incorporate into corporate ISO management processes. | |
Metrics and Targets | • The Sustainability Committee sets climate-related performance indicators and quantitative targets, regularly tracks the achievement rates, and discloses the information to the public. |
• Establish the medium-and long-term targets of taking action toward reducing carbon emissions by 30% by 2030 and achieving carbon neutrality by 2050, respectively. |
III. Management of climate risks and opportunities
To enhance the Board's oversight of major management issues such as climate governance, strategies, and goals, CLC has established 2 functional committees under the Board: the Sustainability Committee and the Risk Management Committee. Given the increasing severity and frequency of climate change risks, we have set up the "Climate Change and Circular Economy Office" under the Sustainability Committee, with the General Manager serving as the convener. This office flexibly integrates cross-departmental working groups to promote the execution of climate governance projects such as TCFD, TNFD, and internal carbon pricing.
In anticipation of climate laws and carbon tariffs being implemented by advanced countries in Europe and the US, as well as Taiwan's upcoming carbon fee, CLC launched the TCFD reevaluation plan in 2023. The scope has been expanded to include all business locations in Taiwan to fully grasp the risks, opportunities, and financial impacts brought by climate changes in the short, medium, and long term. We have identified 6 major transition risks, 2 physical risks, and 4 climate-related opportunities, along with their financial impacts. CLC will continue to take various measures to strengthen risk management and operational resilience, accelerate the deployment of low-carbon development and climate adaptation strategies, and seize low-carbon business opportunities.
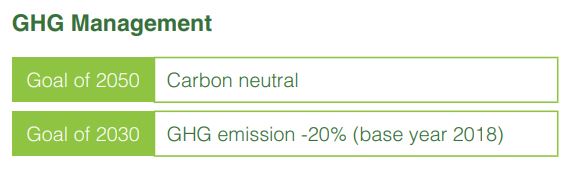
Greenhouse gas emissions decreased by 5.06% from the baseline year, advancing toward net-zero with scientific carbon reduction
In response to global climate change and in line with the national long-term GHG reduction goals, CLC has been at the forefront of its industry. As early as 2004, our Tayuan Mill participated in an Industrial Bureau pilot project. After obtaining the world’s 1st ISO 14064-1 GHG emissions certificate in 2005, we began to extend the successful experience of ISO 14064-1 GHG inventory of Tayuan Mill to all mills/plants in Taiwan in 2006, activating the emission reduction management policy on all production lines across Taiwan ahead of competitors.
In alignment with the national net-zero emissions target, CLC has set long-term goals to take action toward achieving a 20% carbon reduction by 2030 and carbon neutrality by 2050. We have pragmatically proposed 4 scientific pathways to reduce carbon emissions: enhancing energy efficiency, developing renewable energy, deepening the use of circular economy and low-carbon fuels, and innovating the application of carbon-negative technologies. We are actively responding to global decarbonization trends and the green energy transformation goals of our company. In 2023 our GHG emissions in Taiwan were 1,366,142.0487 tCO2e (Scope 1 and Scope 2), 15,071.7980 tCO2e less than 2022 and 5.06% less than the base year. Our company's 2023 GHG inventory is based on the requirements of the ISO 14064-1:2018 standard and has been verified by a third-party verification body according to the ISO 14064-3:2006 standard. The verification is expected to be completed by the end of August 2024, and the fully assured information will be disclosed on the CLC website - Download Center by December 2024.
Our company is actively engaged in carbon reduction actions. The steam system energy conservation project of the paper machine at Tayuan Mill was successfully registered to EPA's GHG offset program in 2020 (79,000 tCO2e). We also completed the monitoring reports and collected related data in 2021. Then, in 2022, we conducted third-party verification and applied for the offset. In the future, we will continue to strive for the GHG offset quota from the EPA as the substantial reward for our efforts in carbon reduction.
For overseas operations in 2023, the GHG emissions from the Binh Duong Paper Mill in Vietnam were 579,240.9157 tCO2e. The Scope 1 and Scope 2 emissions were 549,907.2640 tCO2e and 29,333.6517 tCO2e, respectively. The GHG emissions from the Viet Long Paper Mill in Vietnam were 9,676.4600 tCO2e, with Scope 1 and Scope 2 emissions at 5,443.0900 tCO2e and 4,233.3700 tCO2e, respectively. For the 8 paper mills in Shanghai Chung Hao Plant, China, the Scope 1 and Scope 2 emissions were 5,979.7500 tCO2e and 7,872.3300 tCO2e, respectively, totaling 13,852.0800 tCO2e. The emissions for Gemtech Optoeletronics Corp. were 106.3835 tCO2e for Scope 1 and 1,916.9315 tCO2e for Scope 2, with total GHG emissions amounting to 2,023.3150 tCO2e.
Leading the Industry Alliance in Low-Carbon Transformation and Establishing a Local Carbon Data Database
Facing the global trends of net-zero and carbon-neutral supply chains, sustainable practices cannot be achieved in isolation. Internally, our company is actively and steadily accelerating the low-carbon transformation of the industry chain, led by CLC. Externally, we share practical experience in low-carbon transformation over the long term, striving to assist small and medium-sized enterprises in adapting to the overwhelming sustainability regulations and trends. In response to the government's policy of "big enterprises supporting small ones," in 2023, we joined forces with 20 industry chain partners to establish Taiwan's 1st "Industrial Carbon Neutral Alliance" in the paper industry, building a local industry carbon data database and completing the 1st carbon footprint inventory for industrial paper. By leveraging corporate influence, we have driven over 250 million NTD in carbon reduction investments within the industry chain, contributing to an annual emission reduction of 11,959 Mt and saving over 55 million NTD annually in energy costs, thereby enhancing the overall international competitiveness of the paper industry.
Environmental Management and Environmental Protection Expenditure
Follow the trend of regulations at home and abroad, we explicitly concluded the expenditure and investment in environmental protection and implemented the environmental accounting system in 2001. In 2023, we invested a total of 1.206 billion TWD both domestically and internationally, and we will continue to allocate funds to enhance environmental performance in the future.
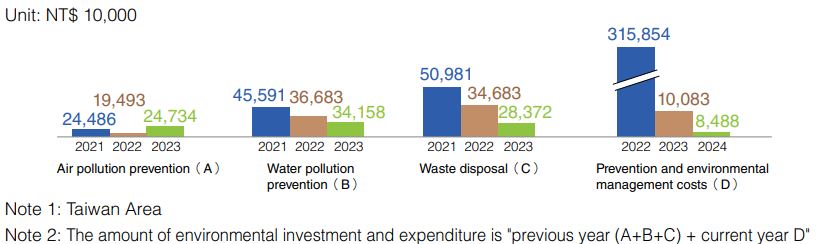
Environmental Management Verification
We have implemented and applied for certification of international management systems at all mills/plants, including the ISO 14001 environmental management system, ISO 14064-1 GHG inventory, and ISO 50001 energy management system. All operational sites in mainland China and Vietnam have implemented the ISO 14001 Environmental Management System. In 2022, the group's subsidiaries also began greenhouse gas inventories and energy management. Eight sites, including the Binh Duong Paper Mill and Yue Long Plant in Vietnam, and the Chung Hao Plant in Shanghai, China, have received ISO 14064-1 and ISO 50001 certifications.
Environmental Fines
In 2023, there were no significant records of fines, but there were a total of 2 cases of missing environmental regulations both domestically and internationally. This includes one case each of water pollution and waste. Measures have been taken to address these deficiencies and prevent recurrence. We have actively addressed deficiencies, prevented recurrence, and continues to carefully manage through digital tools, education and training, improved SOPs, and R&D investments.